Most developers have heard of mass timber by now. They’ve also likely heard that it’s more sustainable yet more expensive than some traditional construction methods. And that’s about as much as most people, even real estate professionals, know about it.
This letter will provide an introduction to mass timber and the practical considerations of using it for new development, especially in the United States. We’ll address the critical items that any developer considering a mass-timber project should consider across various stages of the project, including:
- Underwriting
- Insurance
- Design
- Procurement
Introduction: What is Mass Timber?
Mass timber refers to various engineered wood products made by laminating, gluing, nailing, or doweling multiple layers of solid wood together to create exceptionally strong, precise, and lasting building components. This technology enables the use of timber in tall buildings, making it a viable or even superior alternative to less sustainable structural materials like steel and concrete. Mass timber can be implemented across various building types and asset classes: multifamily, office, educational, public, airports, and even industrial buildings.
Mass timber technology is relatively new. It was popularized in Austria in the late 1980s, and it has only recently been adopted into the International Building Code (IBC) in the 2021 IBC under Type 4 construction. The material is known for its sustainability, as most manufacturers utilize wood from sustainably managed forests. Mass timber is also gaining popularity in mid-rise and high-rise buildings, offering a high fire resistance level due to wood charring at a predictable burn rate.
Although there are many varieties of engineered wood manufacturing methods, for the sake of simplicity, we will focus this article on cross-laminated timber (CLT) and glued laminated timber (glulam). CLT is typically used to create flat panels of various sizes and thicknesses for floor slabs or walls, while glulam products are typically used as beams and columns.
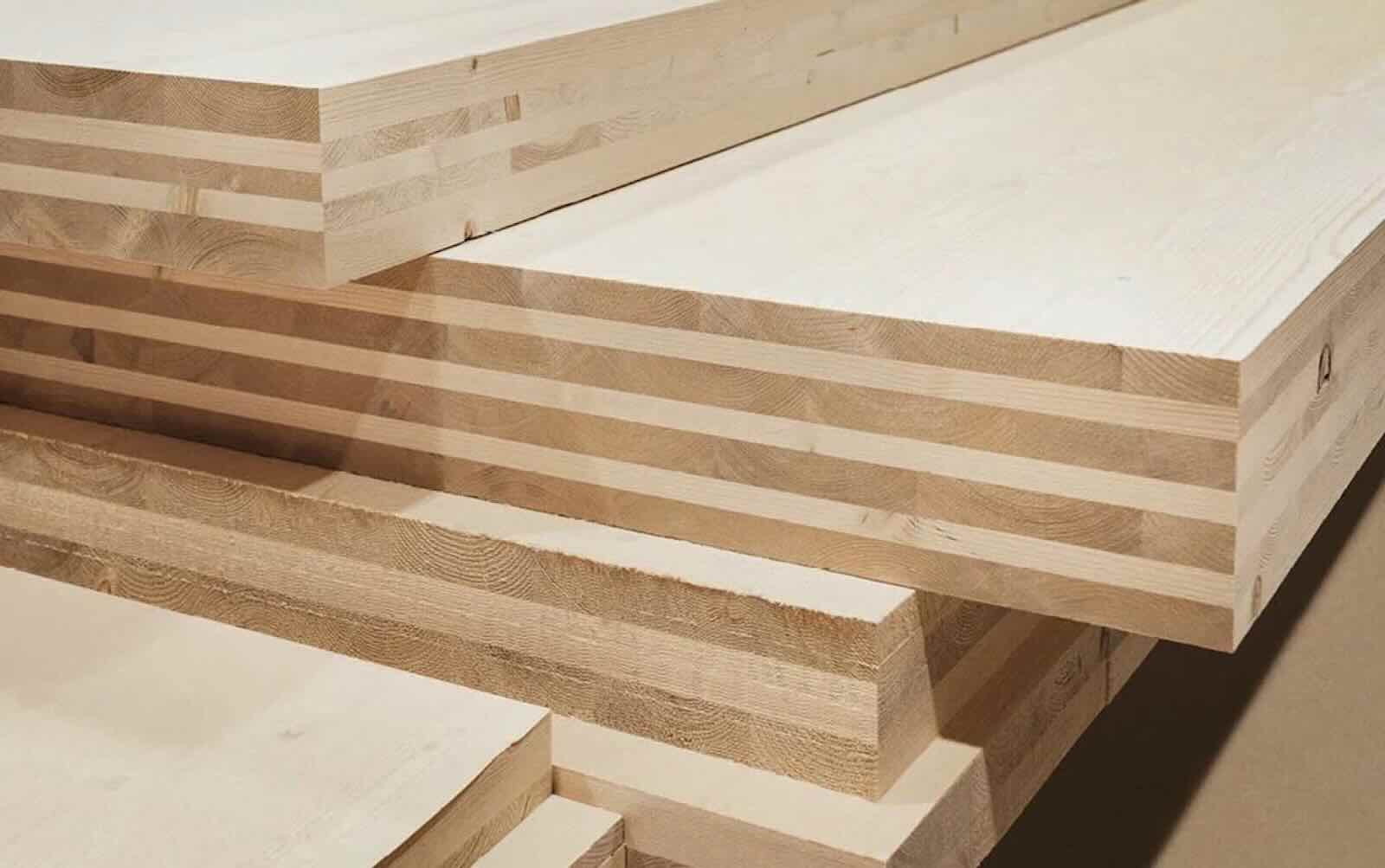
Underwriting
Any construction technology must be financially feasible, whether by generating additional revenue or allowing projects to be built faster or cheaper. One challenge of considering mass timber for new development projects (especially in the United States) is the limited reliable data on its holistic impact on the financial performance of the projects. Some organizations, like WoodWorks, have published materials and case studies on mass timber applications, but even they rarely provide an apples-to-apples comparison of how the same project may have performed using more common construction methods. These comparisons are challenging because the project team must design identical buildings that differ only in the construction materials used.
In order to provide this benchmarking information, Neutral partnered with the U.S.D.A. Forest Service Lab and Soft Wood Lumber Board to compare the performance of four different construction methods on the equivalent design for the same mixed-use development.
The study compared traditional Post-Tensioned Concrete structural frame design, with an All-Steel structure, an All-Mass-Timber structure, and a Mass Timber-Steel Hybrid structure (CLT decks with steel columns) for the same building—a 14-story mixed-use building in Madison, WI, with 206 residential units.
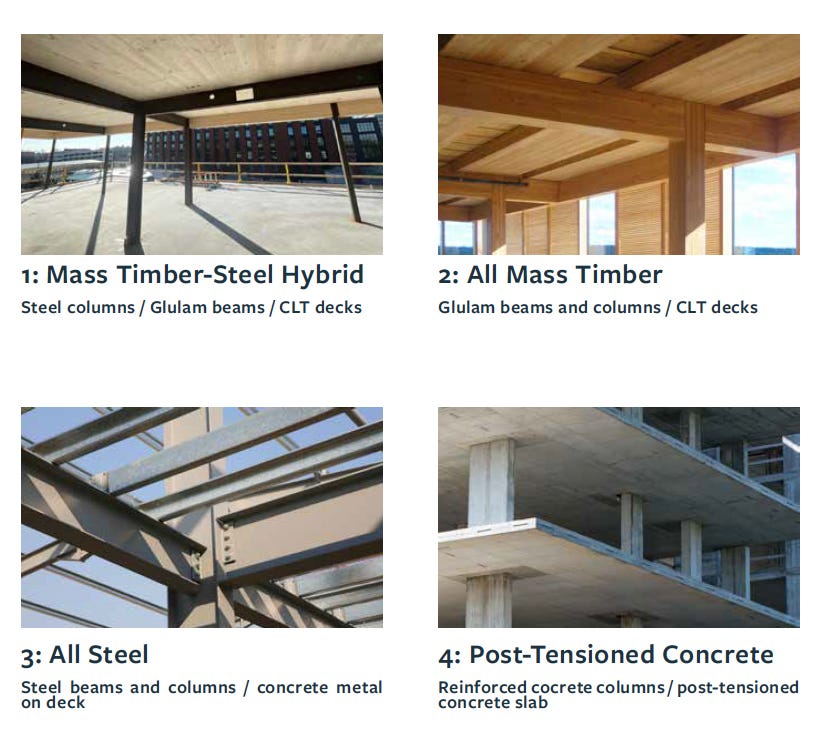
Structural engineers and a general contractor created four equivalent structural schemes, detailed budgets, and schedules for the same building, and a Life Cycle Analysis was conducted to determine the relative carbon impact of each scheme. The cost per square foot estimate factored into the pricing analysis a compression or expansion of the schedule to factor in day-for-day costs like general conditions, general requirements, and equipment.

The findings illustrate the trade-offs and relative strength of each approach. It’s worth reiterating that this comparison data is based on a specific mixed-use building design, in a specific market, and only looks at the structural elements. It shouldn’t be used as a guiding measure for buildings of different scales or asset types (e.g., industrial, office, etc.).
Cost
The Post-Tensioned Concrete structural scheme turned out to be the most affordable option. It’s no surprise then that it’s the most common structural method for new high-rise residential construction. Mass Timber-Steel Hybrid resulted in a comparable cost to All Steel. While the All Mass Timber scheme was the most expensive option (for a detailed look at cost mitigation strategies for mass timber construction, refer to this checklist created by WoodWorks).
Speed
The All Steel structure in this study was the fastest approach to build. It allows for relatively simple, standardized connections, less coordination between trades, and an erection that is not gated by concrete curing. The Concrete scheme required more time for the material to cure. The Mass Timber-Steel Hybrid scheme took longer than the All Mass-Timber scheme due to the need to coordinate and switch between various trades on each floor before moving up. Additionally, the fireproofing of the steel members on each floor adds time compared to the All Mass-Timber scheme.
By contrast, WoodWorks’, an industry organization promoting the use of mass timber in construction, indicates that the Mass-Timber structures can be constructed with up to 25% savings in structure erection schedule. This may be more relevant for low-rise rather than high-rise construction. General statements about mass-timber savings on the overall construction schedule are not possible now, and a detailed schedule study for individual projects would be recommended.
.jpeg)
Sustainability
Where both All Mass Timber and Mass Timber-Steel Hybrid approaches shine is sustainability and reduction in kilograms of carbon dioxide per square meter (kg CO2e/m2). The system allows for up to 20% reduction in embodied carbon compared to using concrete. This is a very conservative estimate because the Life Cycle Assessment methodology used only accounted for materials during construction, without their end-of-life stage. The Mass Timber-Steel Hybrid scheme results in a 46% reduction in carbon emissions using the static accounting method for biogenic carbon. The All Mass Timber achieves up to 60% reduction in carbon emissions compared to a baseline code-compliant Post-Tensioned Concrete scheme.
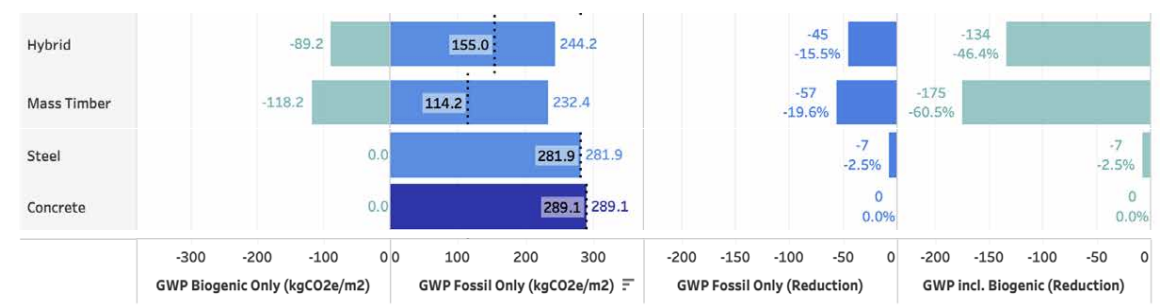
Despite its obvious sustainability benefits, it may not be clear why developers would choose to use mass timber in their projects, given the cost advantages of concrete and the speed advantage of steel. However, a number of short—and long—term financial considerations can make building with either a full or a hybrid mass timber structure financially feasible and even strategically beneficial.
Income
Construction costs are only one of the aspects influencing the overall financial performance of a project. Developers should also consider the additional income a mass timber project can generate.
There's growing evidence that mass timber projects can command a rental premium. A comparison of recent deliveries across several markets shows a 2% to 18% rental premium for mass timber projects. There are several possible explanations for this premium, including the visual allure of exposed timber in interiors, the increasing importance of carbon reduction and sustainability for specific renter demographics, and the possibility that some renters are drawn to the aroma of timber over concrete.
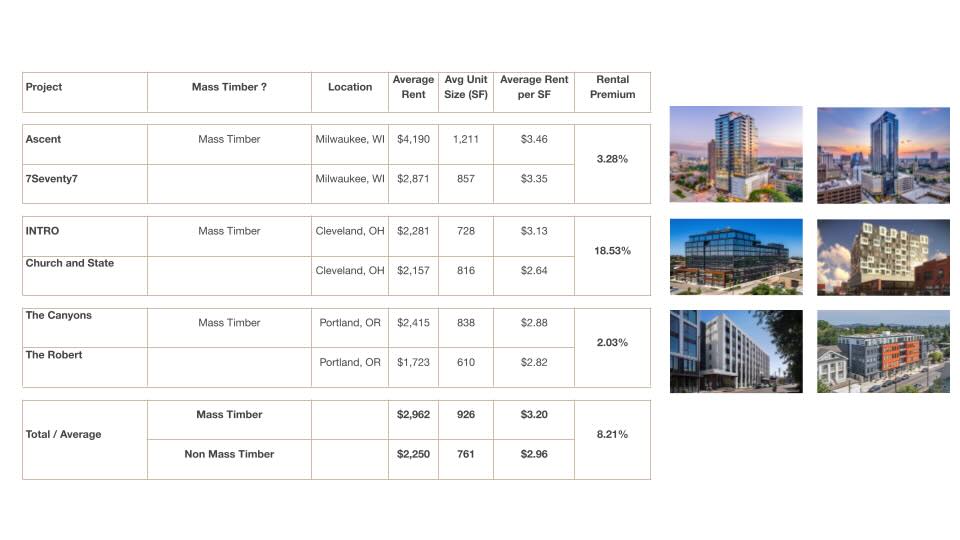
An even more striking example is Super Bungalows, a 12-unit multifamily project by Super.la and the first mass-timber multifamily building completed in Los Angeles. The project commands rents 30% higher than comparable units in the neighborhood and reached full occupancy within approximately 2 weeks of leasing start. This project has an exceptional overall design, so mass timber would not be solely responsible for the rental premium, but it certainly played a significant part.
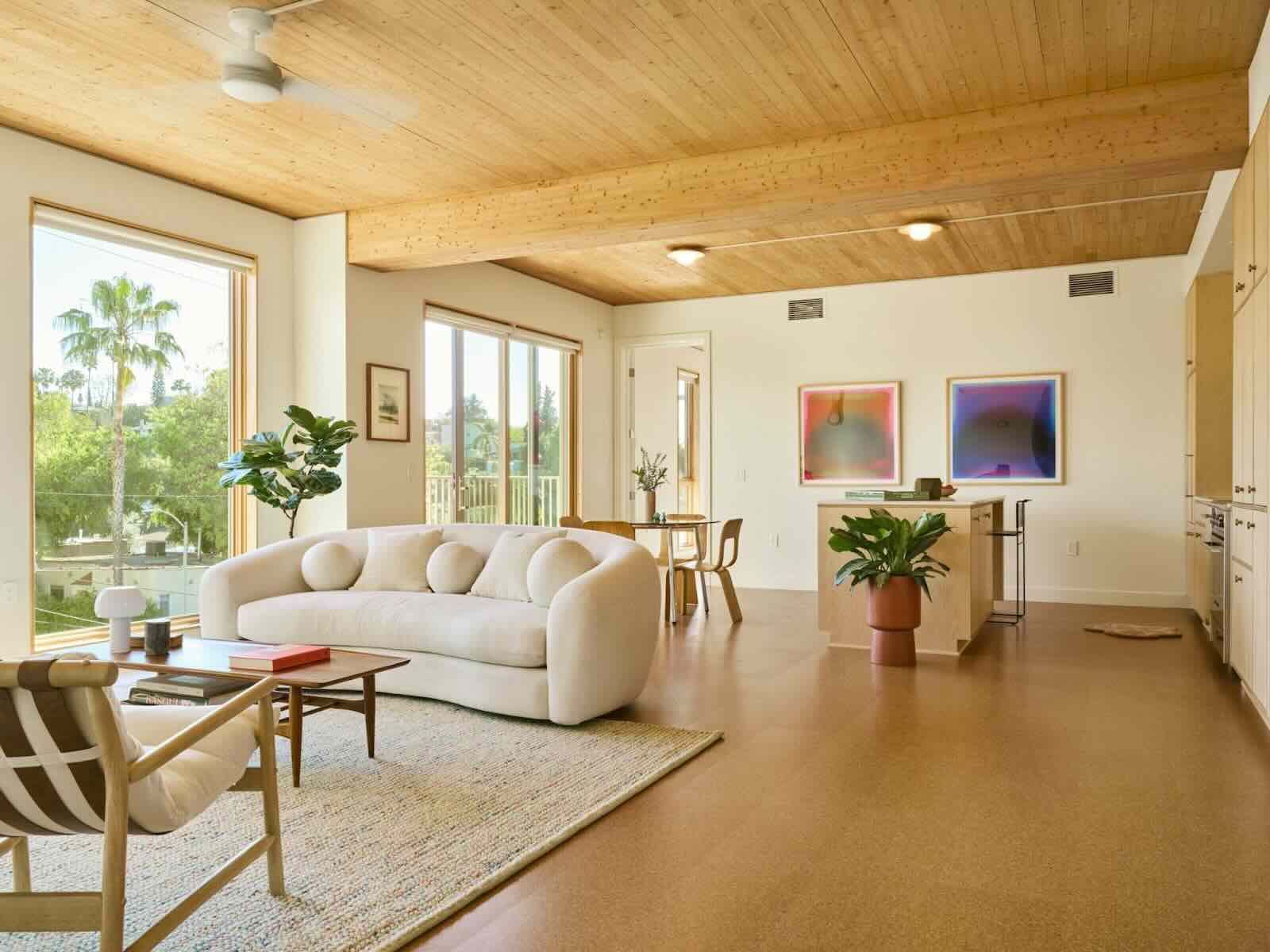
Sale / Exit
An increasing number of institutional investors worldwide – mainly in Europe but also in North America – are implementing environmental, social, and governance (ESG) standards for new as well as existing assets in their portfolios. This is in response to government regulations and investor-imposed impact mandates.
For real estate, these mandates mean that within the next ten years, there will be an imbalance in supply and demand between institutional demand for sustainable assets and their relative lack of supply in the North American market.
This imbalance creates an opportunity for developers to meet the coming demand by building sustainable assets today. For long-term holders, the benefits of paying more for sustainable building technologies up front could be justified by a compression on cap rates at sale, driving the purchase price up and thereby bringing higher returns to the project investors.
Insurance
Unfortunately, many insurance companies perceive mass timber construction as riskier than steel and concrete. In some cases, insurance carriers will not write the risk and will therefore exclude any mass timber buildings from their portfolios. In other cases,the insurance carriers will place a significant premium on any mass timber building. These insurance challenges will appear both during construction as well as upon completion and stabilization.
Neutral’s 14-story mixed-use building in Madison, WI addressed these challenges through a quota share–a pro-rata reinsurance contract in which the insurer and reinsurer share premiums and losses according to a fixed percentage. This strategy was successful, and the project was insured by Zurich, CNA, Chubb, and two reinsurers. Zurich is a good lead insurer for developers who plan to use a quota share approach because they have an extensive mass timber application drafted and a comprehensive contract that all other carriers will accept.
Design
Assembling the Team
While awareness of mass timber applications in new construction is growing, the number of professionals who have worked on a mass timber building is small. Therefore, it is crucial for developers who are considering using mass timber to assemble a consultant and contractor team with experience in designing and constructing mass timber structures.
As recently as the mid-2010s, some manufacturers had to establish subsidiary structural engineering consulting practices to assist clients with mass timber engineering due to a lack of available experts in the market. But today there’s a growing number of structural engineering, architectural, acoustical consultants as well as general contractors with experience in mass timber. Josh Dortzbach, Founding Principal of FOREFRONT Structural Engineers, explains the importance of involving mass timber experts early in the project:
“Developers need cost certainty early in the life cycle of a project. Because our industry is still in the early adoption cycle of building with mass timber, there are many different possible solutions which drive cost. These solutions depend heavily upon a structural engineer’s ability to understand both the limitations and the opportunities of the manufacturing process in order to bring cost certainty to a project.
You need to get that certainty and lock in a supplier before Schematic Design starts. This means that the structural engineer should be an equal partner earlier in the project cycle at the concept phase to help navigate common pitfalls.”
Compliance
Developing with mass timber, just like with any other construction material, requires compliance to all applicable building and fire codes for design. In case of mass timber buildings, this is further complicated by rapidly changing code provisions, as well as inconsistent adoption and interpretations by various jurisdictions.
International Building Code (IBC) defines five construction types that dictate where and how mass timber can be used without a variance from the local authority having jurisdiction (AHJ). Types III, IV, and V allow for the use of mass timber throughout the structure for buildings of different heights.
Until recently, the 2021 IBC was the first to include the primary provisions associated with the new types of mass timber construction. The 2024 edition of the IBC includes a change that allows Type IV-B construction to have 100% of the mass timber ceilings exposed.
Certain states and local AHJs are reluctant to adopt and embrace 2021 and 2024 IBC provisions which may be a limiting factor for widespread mass timber adoption in North American construction in the foreseeable future. Developers should pay close attention to and consult with local AHJs on their code interpretation to gauge its impact on project design, required approvals, potential variances, and project timeline.
Acoustics
Mass timber has different acoustic properties compared to concrete and steel structures. In addition, the desire to keep portions of timber exposed for aesthetic reasons reduces the amount of drywall and other ceiling finishes that would traditionally contribute to sound dampening.
This makes acoustics an important consideration for developers in both the design of the building and its cost estimation. Certain solutions, like acoustic floor mats or raised floors, may have a significant impact on costs. Developers should retain acoustic consultants or work with engineering consultants who can provide this expertise in-house.
Moisture
Every construction material has its unique requirements and weather dependencies. For example, steel and concrete have weather dependencies; contractors can't pour concrete when it is too hot or cold, or rain could affect the concrete's cure time. Steel can degrade with too much water and exposure to nature's elements for too long. Mass Timber also has unique challenges, in which moisture poses the most significant concerns before, during, and after construction. Mass timber structures need extensive moisture management during shipping and on-site assembly. Building science consultants should develop a moisture management plan ("MMP") for a mass timber project. In particular, the following areas may require special moisture management treatment:
- Areas with no roof above with precipitation expected during exposure duration,
- Areas with a roof above but open perimeter with wind-driven precipitation expected during exposure duration,
- Areas with extended exposure timelines that increase the risk of wetting potential,
- Slab edge detailing on every floor of mass timber; and
- Spine joint details where the CLT panels meet one another.
For Neutral's 14-story mixed-use building in Madison, WI, the team created an MMP to ensure the least amount of moisture intrusion during the structural assembly and enclosure period of construction. A few essential procedures were a temporary roof on every other floor, Siga Wetguard sealants applied to the CLT panels in fabrication, Rothoblaas tapes, adhesives, and membranes applied on site, and NISUS Bora-Care to prevent mold and fungi growth once the building is complete.
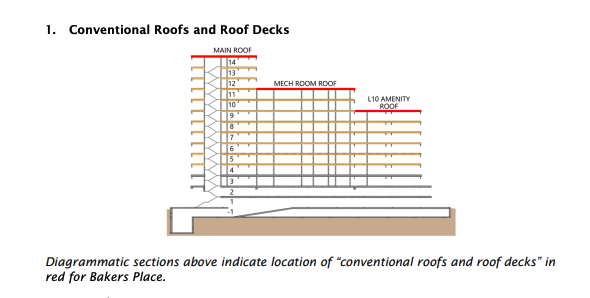
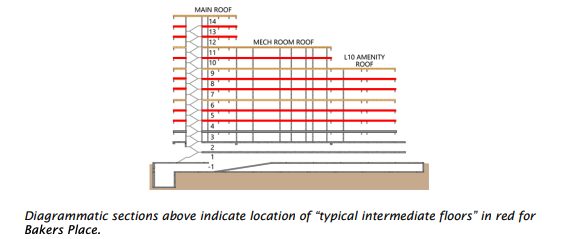
Construction planning
The most critical risk for any mass timber project is the level of experience of the general contractor and, more importantly, the Installer of the material. Given that the construction method is relatively new, it has unique nuances for the Installer, unlike other wood structures, such as Type III (stick frame construction), or steel and concrete. The development of a moisture management plan is crucial, but its effective implementation is equally vital. The difference between a GC and an installer who has worked with mass timber and understands the implications of moisture infiltration, and one that does not, could be the difference between a building free of fungi and mold, and one that is not.
Procurement
Developers building with mass timber should treat the product as a long lead item and consider potential vendors very early in the design process. Varying building design and product requirements (dimensions, thickness, visual quality, etc) may mean that different vendors will be competitive.
In some cases, manufacturers have standard dimensions for their products that they produce in volume resulting in noticeable cost savings. Knowing these specifications and trade offs early on is critical for design and cost optimization. For example, KLH, a large mass timber supplier based in Austria, fabricates what they call “blanks” to sell in mass quantities to the Austrian timber and carpentry market. Their typical dimensions for these blanks are 11 feet 11 inches by 11 feet 11 inches, or you can have them fabricated in 12 feet, 18 feet, or even 36 feet long.
In the case of Bakers Place, Neutral bid out the project to six manufacturers. Three in North America and three in Europe. The European manufacturers' bids ended up being roughly ~16% lower in total cost (inclusive of shipping) than the closest North American manufacturers' bid.
This is not a universal rule or outcome and it always makes sense to bid out the project to multiple potential vendors. In addition, software companies like Generate are now trying to simplify this process by comparing multiple vendors and mass timber products within their software platform.
Here’re some mass timber suppliers that developers can consider (not an extensive list):
- Sterling — USA (IL, TX)
- Mercer — USA (WA, AR), Canada
- Smartlam — USA (MT, AL)
- Freres — USA (OR)
- Element5 — Canada
- Kalesnikoff — Canada
- Nordic — Canada
- SODRA — Canada
- Binderholz — Austria, Germany
- KLH — Austria, Germany
- Stora Enso — Finland
- Sodra — Sweden
Conclusion
Mass timber is a promising sustainable alternative to traditional construction methods, but we’re still in the early days of its adoption. Using novel material presents new challenges from design to compliance, insurance, and weather protection.
Despite all the complications, the excitement from renters, buyers, and media may help offset its relatively expensive price. Long term, the growing demand from impact investors will result in a premium for sustainable real estate assets.
For some thesis driven developers this can make mass timber implementation worth the effort.
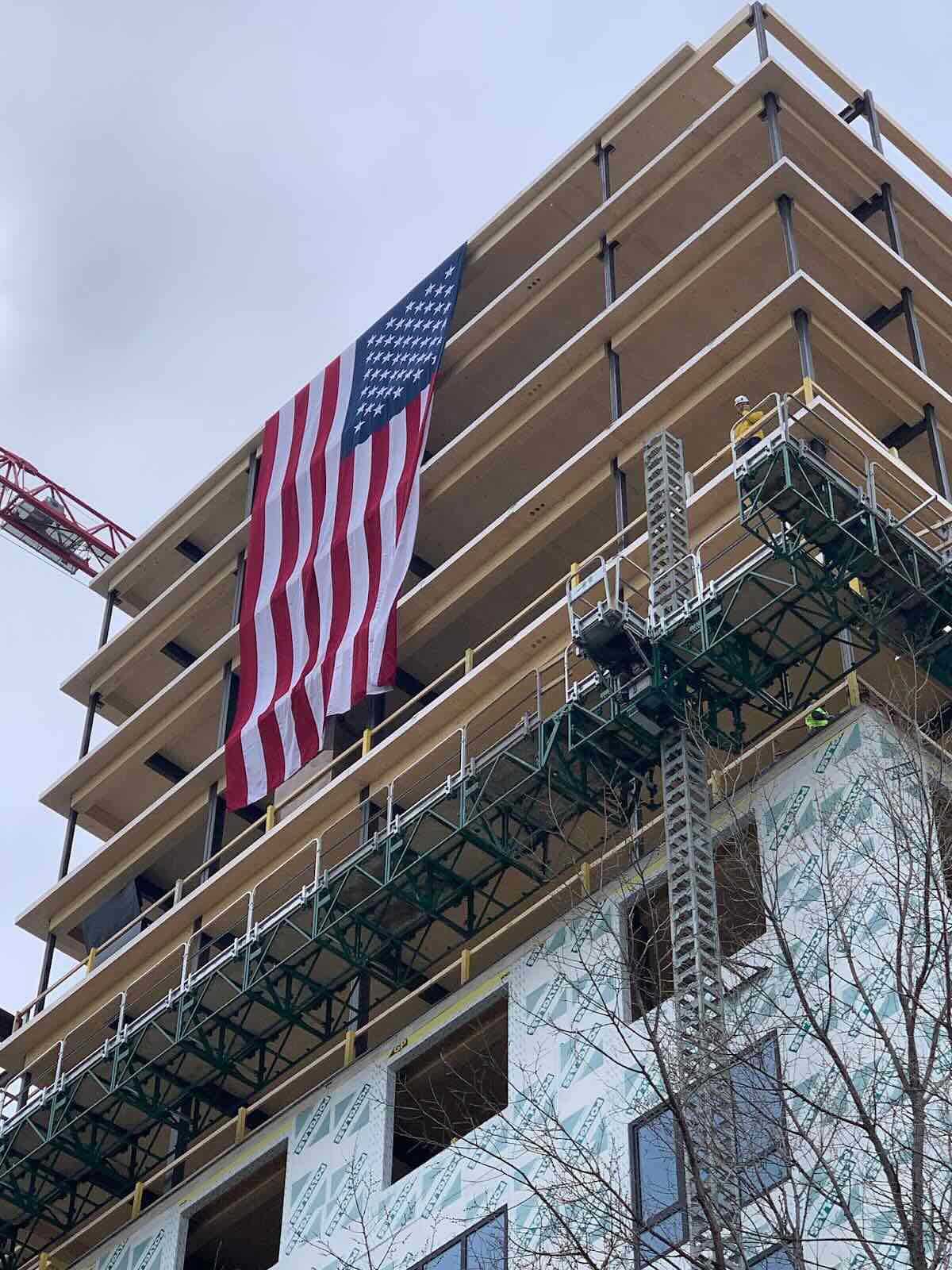